It is a very controversial issue for the power harness processing factory to do a good job in quality management. When we often communicate with the quality manager of the factory, we often hear that they are complaining or are busy.
If "busy" is transformed into "prevention", the complaints of external customers are often that internal quality control is not in place. If quality is to be done well, it is necessary to prevent on-site problems, eliminate problems in the bud, and prevent problems .
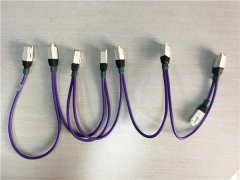
How to "prevent"? Three inspections should be done before the process: first inspection, patrol inspection and final inspection.
Front process characteristics: high degree of automation, key position, relatively stable quality, but once a problem occurs, it may be batched and the RPN value is high. In addition to the regular TPM inspection of the equipment every working day, employees also need to do the "three inspections" during the production process.
In the terminal crimping operation, the front and rear foot height and width dimensions and the tension are the key control items. The first and last inspections and patrol inspections of each shift must record the corresponding values.
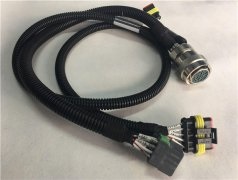
First inspection, inspection before the start of the shift, mass production can only be carried out after the first piece is press-fitted, otherwise the equipment needs to be debugged until it is qualified. Inspection is an indispensable part. Inspection is generally an inspector in the QC department. The purpose of inspection is to ensure the stability of terminal crimping and reduce quality risks.
Final inspection is an easily overlooked link. Employees are often busy off work or switching materials, neglecting the inspection of the final piece. The purpose of the final piece inspection is to change the number of crimped batches and facilitate future batch traceability. The power harness processing plant grasps every level of management and strives to achieve quality greater than efficiency. You can choose with confidence!